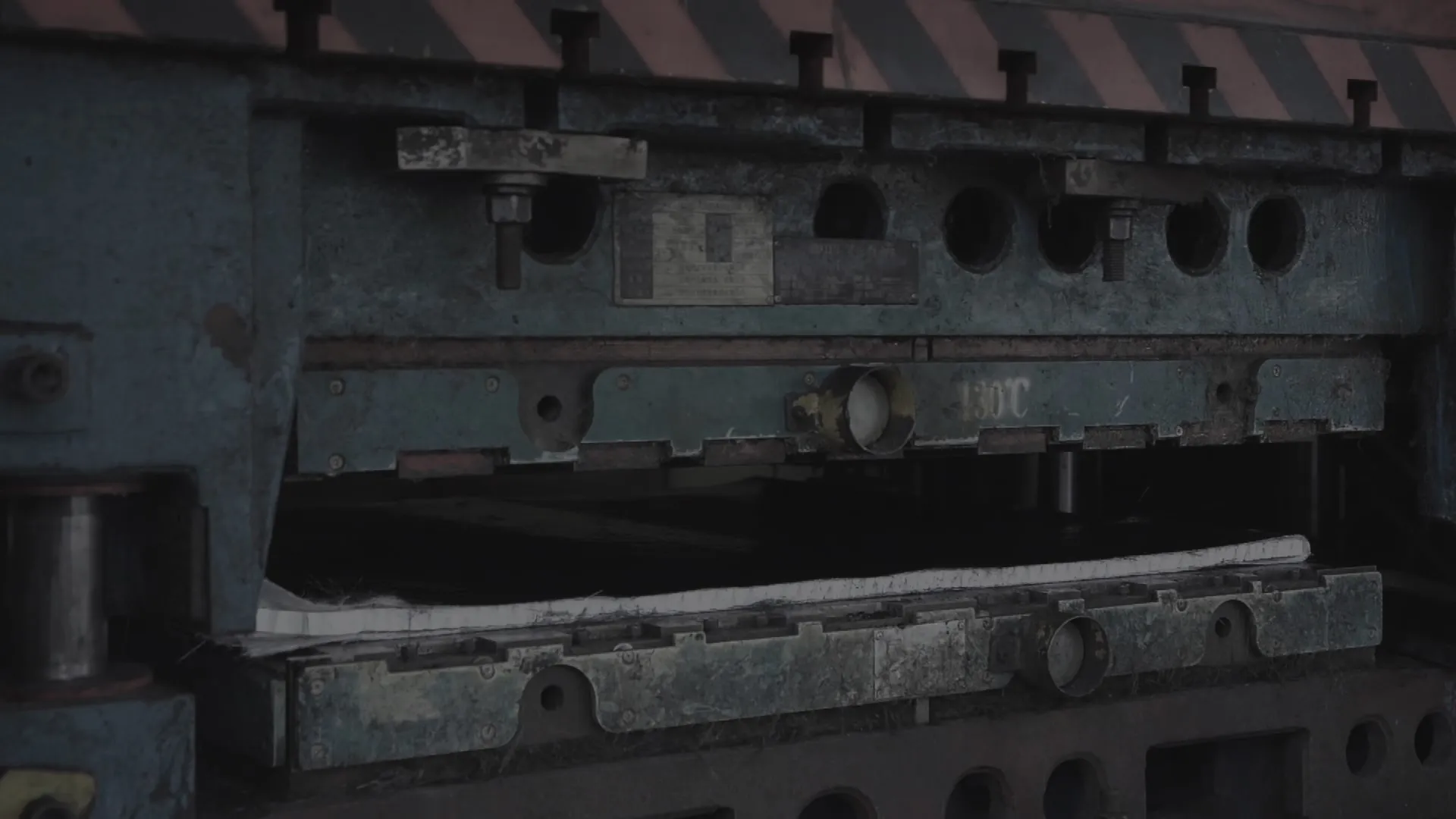
Carbon Fiber Mold.
- Suase /
- Composite Tooling /
- Carbon Fiber Mold
This is your ultimate guide to understanding carbon fiber molds and their key role in modern manufacturing.
A carbon fiber mold is a specialized tool used in the production of composite components. It helps shape and harden carbon fiber materials to make them strong, lightweight, and durable. These molds are critical for industries where strength, lightweight properties, and durability are paramount.
The process of creating a carbon fiber mold involves several key steps, each of which requires precision and expertise:
- Design and Prototyping: Engineers use CAD software to design the mold, ensuring accuracy and feasibility.
- Master Mold Creation: A master mold, typically made of wood or metal, is crafted as a reference for the carbon fiber mold.
- Lay-Up Process: Layers of carbon fiber fabric are applied over the master mold, impregnated with resin, and carefully aligned to prevent defects.
- Vacuum Bagging: The mold is sealed in a vacuum bag to remove air and compact the layers, ensuring a high-quality finish.
- Curing: The mold is put into an autoclave (a kind of pressure cooker) or oven to make the resin solid and get the mold into its final form.
- Finishing: The mold is sanded, polished, and inspected for any imperfections before use.
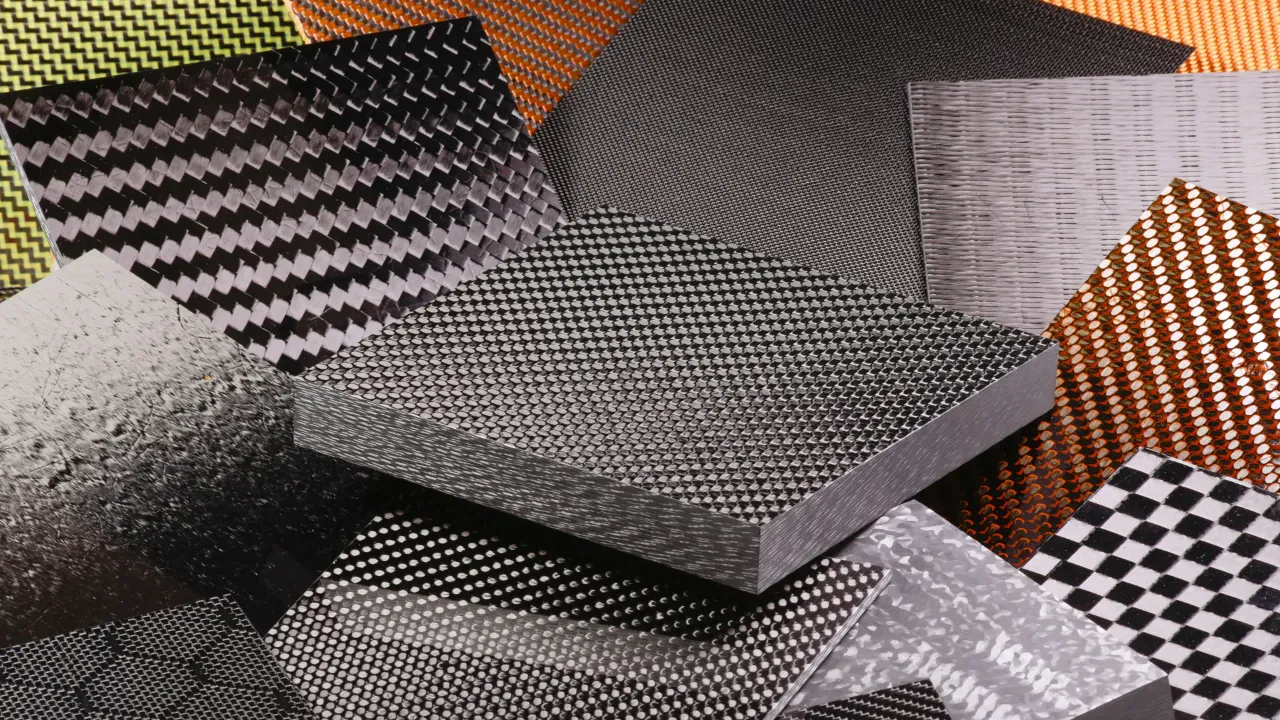
Carbon fiber molds offer several benefits, making them a preferred choice for high-performance applications:
- Lightweight and Durable: Carbon fiber molds are much lighter than traditional molds, which makes them easier to handle while maintaining exceptional strength.
- Precision: The high rigidity of carbon fiber ensures that the molds make products that are the same size every time.
- Thermal Stability: They can also resist high temperatures, making them suitable for complex curing processes.
- Corrosion Resistance: They are also resistant to corrosion, which means they won't rust or break down easily.
Carbon fiber molds are used across various industries, including:
- Aerospace: Making lightweight parts like wing parts and fuselage sections.
- Automotive: Making body panels, hoods, and structural parts for high-performance vehicles.
- Sports Equipment: Making high-end bicycles, tennis rackets, and protective gear.
- Renewable Energy: Making wind turbine blades and other energy-efficient parts.
- Medical Devices: Making custom prosthetics and parts for medical imaging equipment.
While there are many advantages to using carbon fiber molds, there are also certain challenges:
- Cost: The raw materials and manufacturing processes for carbon fiber molds are more expensive than traditional methods.
- Complexity: High levels of skill and precision are required to ensure that the molds are defect-free.
- Time-Intensive: It also takes a long time to cure and finish the molds, which can delay the overall production schedule.
The future of carbon fiber molds looks good. There will be improvements in automated lay-up systems, 3D printing technologies, and resin formulations. These improvements will lead to faster and cheaper production methods.As more and more people want lightweight and sustainable materials, carbon fiber molds will continue to play a crucial role in the evolution of modern manufacturing.
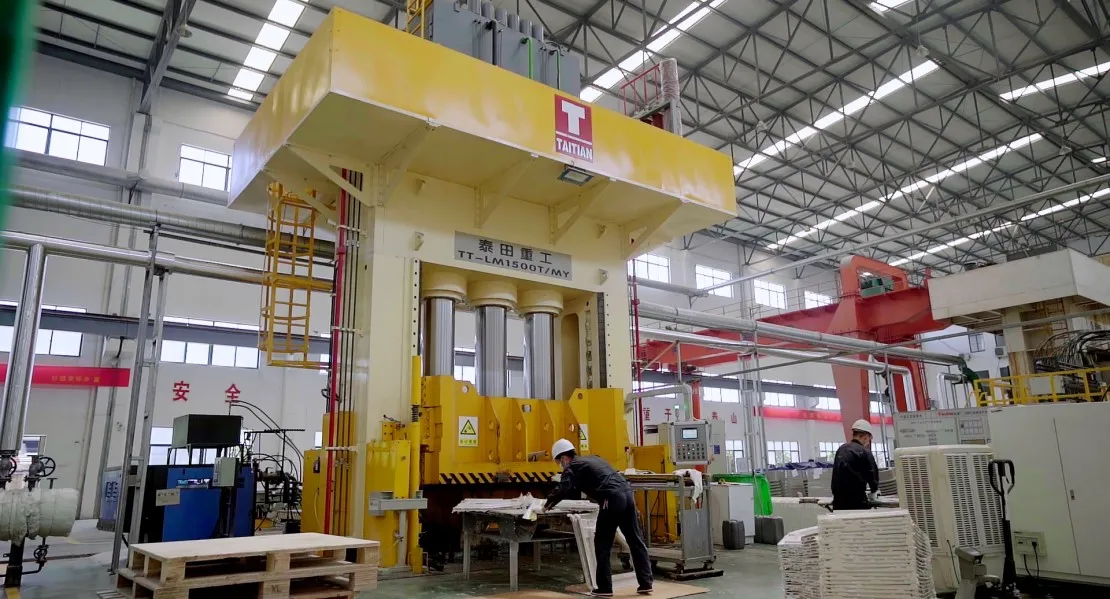