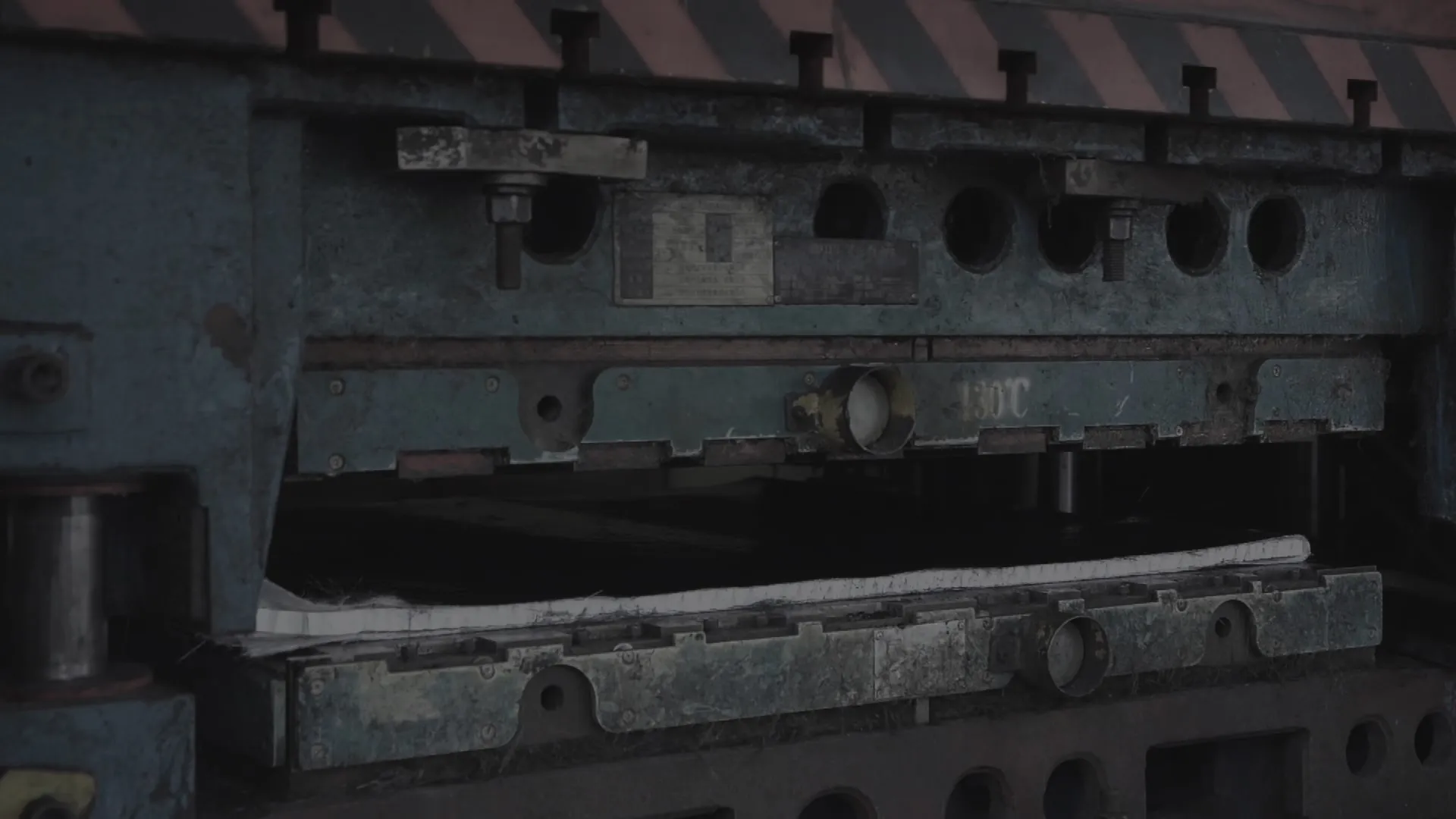
COMPRESSION TOOLING.
- Suase /
- Composite Tooling /
- COMPRESSION TOOLING
What is Compression Molding?
Compression molding is the process where a heated rubber material is placed in one side of a mold, then the other side of the mold is clamped down, and the rubber material is compressed into the desired shape. The mold must also be heated, as the combined compression and heat is what causes the rubber to take its new shape. The mold also has to be designed to meet certain accommodations. For example, the mold needs to have overflow grooves built into it. Since it is difficult to accurately predict the amount of rubber material needed without any overflow, it is better to error on the safe side and use a little extra material to ensure the mold is filled and the piece is molded correctly. This means that every piece will have flash that needs to be trimmed.

Features of Compression Molding
High Volume Programs
Short (2-4 minute) cycle times and the use of machined tool steel molds support annual program volumes to >500,000 units.

Best Tolerances in Process Suite
High dimensional stability of SMC formulations and the use of precision matched-die tooling produce highly-stable and predictable part dimensions that, in turn, can produce tight-tolerance assemblies.
Class A Surfaces
The use of precision matched-die tools that can be polished to mirror finish give the capability to achieve automotive-grade Class A surfaces that can support topcoat finishes.
Wide Range of Material Properties
A wide range of material properties can be obtained with sheet molding compounds by varying the fiber content, filler materials, and performance additives. Materials can be optimized for weight, strength, environmental resistance, economy and many other attributes.
Benefits of Compression Molding
One of the biggest benefits of compression molding is cost. Compared to other processes like plastic injection molding, creating a mold is a lot cheaper. When creating a mold for compression molding, you don’t have to worry about creating gates and runners. You also won’t need to complete a mold flow analysis.
Second, it is cheaper and easier to create larger parts. Generally, with other manufacturing processes, it gets significantly more expensive as part size increases. For example, with plastic injection molding, not only do you need to create a larger mold, but you also need to increase the total clamp force a machine can produce. With compression molding, you don’t need to significantly increase the pressure of the machine when you make larger parts.
The thickness of parts can vary quite a bit – you can easily produce parts that are between 1.3 mm thick to 1 inch. You are also able to get seamless design features with compression molding – you don’t have to worry about the flow lines or knit lines that may appear in injection molding.
Disadvantages of Compression Molding
One of the issues with compression molding is the long cycle times. One cycle can take up to several minutes as a technician has to manually place the material into the mold, heat it up, apply pressure and then wait for the mold to cool off enough to remove the part.
Parts require additional work after they are molded. By the very nature of compression molding, parts will have flash, so there is an additional step of removing the flash.
Another issue is that compression molding isn’t the best choice for complex designs. Simple designs can be easily filled, but complex designs can leave sections underfilled.
Raw Materials used in Compression Molding
Materials that are typically manufactured through compression molding include: Polyester fiberglass resin systems (SMC/BMC/PCM), Polyurethane honeycomb & fiber composite (PHC), Long fiber reinforced thermoplastics (LFT) and Glass fiber mat reinforced thermoplastics (GMT)
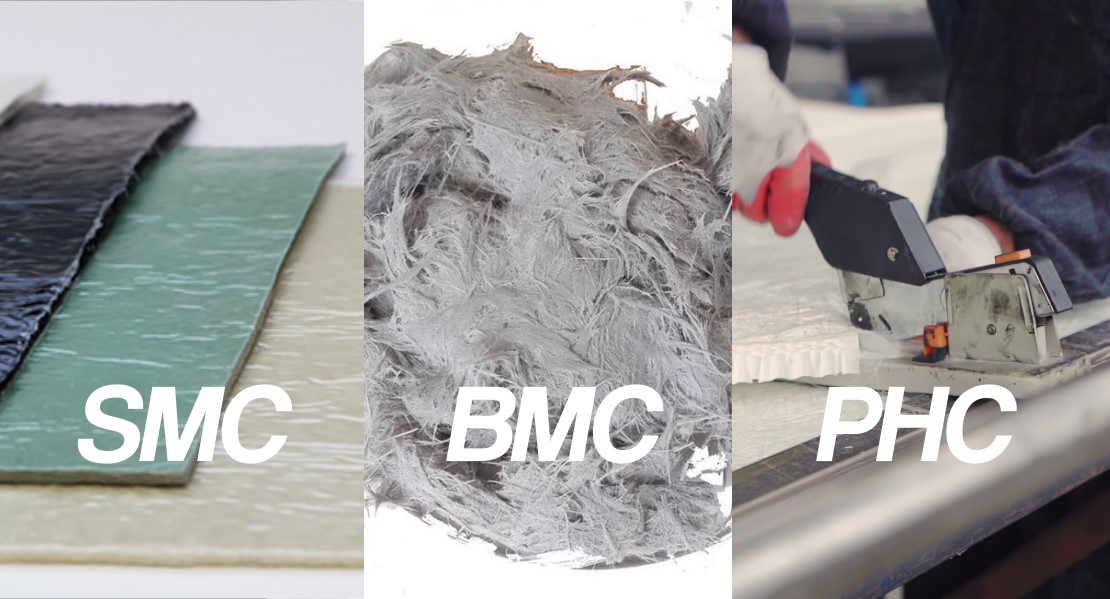
Structure of Compression Mold
The difference with the injection mold is that the compression mold has no pouring system, and the mold is equipped with a feeding chamber. There is a heating device in the cavity or feeding chamber. The structure of the compression mold can be divided into the following major parts.
(1) Cavity part. The cavity is the location where the part is directly formed, where the mold cavity is composed of a punch, a core, and a cavity.
(2) The feeding chamber is different from the injection mold. There is a feeding chamber containing raw materials above the compression mold cavity.
(3) Heating and cooling system. Thermosetting plastic compression molding needs to be performed at a higher temperature, so the mold must be heated. Compression molds are usually heated by electric heating.
In addition, like the injection mold, the compression mold is usually also provided with a guide mechanism, a demoulding mechanism, a lateral split core pulling mechanism, etc.
Design of Compression Mold
When designing a compression mold, it is necessary to design the cavity according to the size and molding method of the product, besides, it is also required to select the appropriate steel according to the quality requirements and demand of the product surface. Compression mold should be made of mold steel with easy cutting, compact structure and good polishing properties. Such as P20, 718, 1.2738 (adjust freely), etc. In addition, it is necessary to consider the related problems of machining accuracy and control the dimensional tolerance, shape tolerance and surface roughness
In order to improve the wear resistance and corrosion resistance of compression mold surface, surface treatment is usually carried out. Chromium plating is one of the most common methods. Chromium plating can keep metallic luster for a long time, and it is stable in various acidic media without chemical reaction. Chromium plating has excellent wear resistance and high heat resistance. When the temperature reaches 500℃, there is no obvious change in its appearance and hardness. In addition, nitriding treatment can greatly improve wear resistance.
The parting line design of compression mold should be easy to demoulding, and the way of simplifying the ejection mechanism can be adopted. When the radial dimension of the product requires high precision, the influence of flash thickness on the dimensional accuracy of compression products should be considered, and the vertical parting line can easily ensure the dimensional accuracy of the product
Compression mold temperature directly affects product quality and production efficiency, and the temperature design of compression mold is usually between 140℃ and 160℃. The heating system includes electric heating, steam heating and oil heating. When designing the temperature system of the mold, choosing the appropriate heating method and ensuring the uniform surface temperature of the mold can reduce the deformation and improve dimensional stability.
In the compression mold design stage, new mold software (CAD/CAM, etc.) is used to master the whole process of compression mold design, manufacturing, assembly, inspection, testing and production, including mold design and manufacturing cost estimation, mold assembly evaluation, mold parts manufacturing process evaluation, mold structure and formability evaluation.
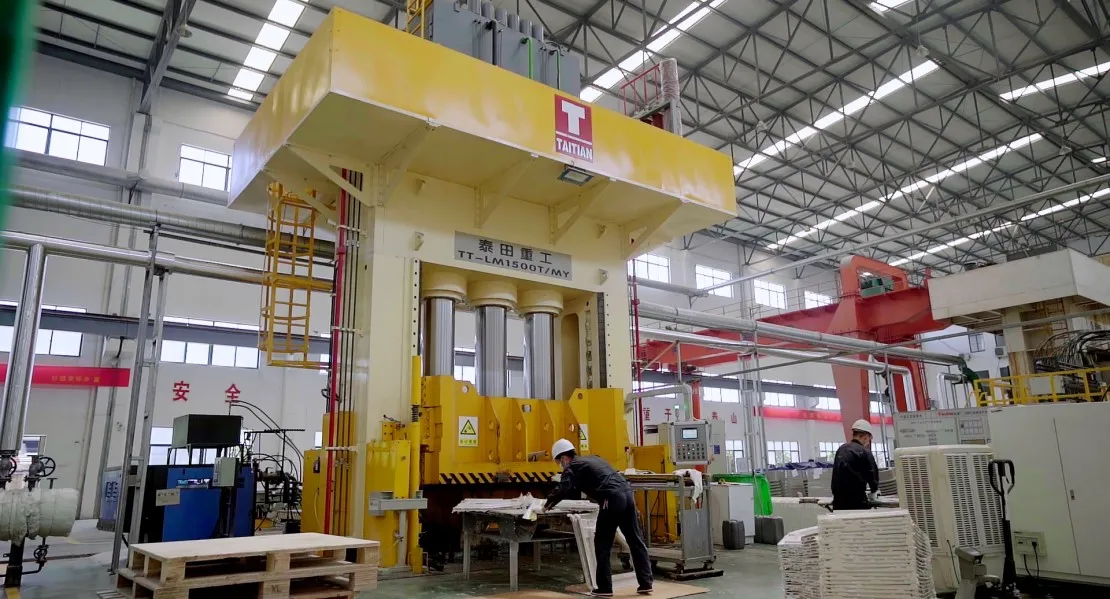