Introduction
Thermoplastic carbon fiber composites are transforming the way modern industries design and manufacture high-performance parts. These advanced materials combine the strength and stiffness of carbon fiber with the formability and recyclability of thermoplastic polymers, making them ideal for lightweight, durable, and eco-conscious applications.
What is Thermoplastic Carbon Fiber?
Carbon fiber is known for its outstanding strength-to-weight ratio. When embedded in a thermoplastic matrix such as PEEK, PPS, or PA6, it forms a composite that is lightweight, durable, and recyclable. Thermoplastic carbon fiber boards are especially valued in industries that demand both performance and efficiency, including aerospace, automotive, consumer electronics, and sports equipment.
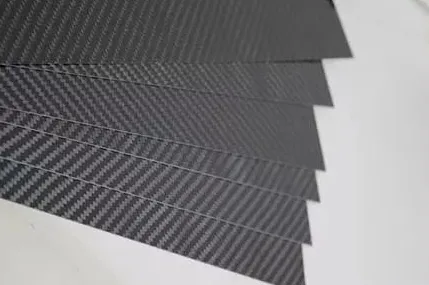
Molding Technologies for Thermoplastic Carbon Fiber Boards
Compression Molding
Compression molding involves placing carbon fiber prepregs into a heated mold and applying pressure to shape the material. It offers short cycle times and high surface finish quality, making it suitable for automotive panels, enclosures, and structural components.
Thermoforming
Thermoforming heats the laminate to a pliable temperature before molding it into the desired shape. This method allows for the production of large, thin-walled parts and is popular in industries requiring fast, cost-effective production.
Injection Overmolding
This hybrid technique combines injection molding and composite sheet forming, enabling the integration of functional features into carbon fiber parts. It's ideal for manufacturing complex, lightweight components with embedded mounting points or ribs.
Advantages of Thermoplastic Carbon Fiber Composite Molding
- Lightweight & High Strength: Ideal for structural applications where weight savings are critical.
- Recyclability: Thermoplastics can be remelted and reshaped, supporting sustainable manufacturing.
- Fast Production: Shorter cycle times enable high-volume manufacturing with lower energy consumption.
- Impact Resistance: The thermoplastic matrix provides enhanced toughness for crash and impact scenarios.
- Chemical Resistance: Excellent resistance to moisture, oils, and solvents, extending product lifespan.
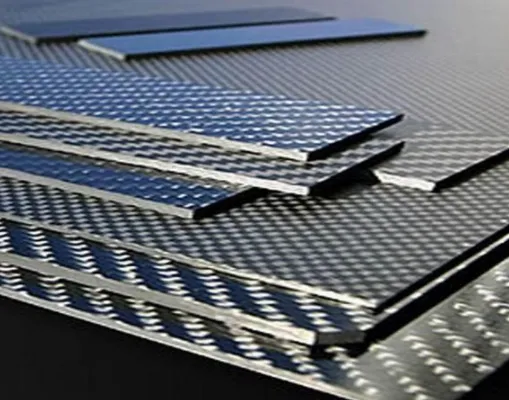
Applications Across Industries
Thermoplastic carbon fiber boards are widely used in:
- Automotive: Door panels, underbody shields, seat frames, and EV battery enclosures.
- Aerospace: Cabin panels, UAV frames, satellite structural parts.
- Sports: Lightweight bicycles, skis, snowboards, and helmets.
- Consumer Products: Tool housings, electronic enclosures, appliance components.
Challenges and Technological Innovations
While thermoplastic carbon fiber molding offers numerous advantages, challenges such as high material costs, processing precision, and capital investment exist. However, the use of digital simulation, automated lay-up systems, and hybrid forming techniques is helping overcome these barriers, driving broader adoption.
Future Outlook
As demand for recyclable and high-performance composites increases, thermoplastic carbon fiber technology is expected to grow rapidly. Future innovations will focus on high-temperature polymers, automation, and integrated molding processes, enhancing cost-efficiency and product complexity.
Conclusion
Thermoplastic carbon fiber board composite molding is a cornerstone technology in modern lightweight manufacturing. Offering strength, recyclability, and efficient production, it is increasingly favored in industries where performance and sustainability are key. With ongoing research and development, its potential is expanding into more advanced and diversified applications.