What is the Temperature of Thermoset Mold? | Thermoset Compression Molding Guide
- Suase /
- SUASE NEWS
Thermoset molding is a high-precision manufacturing process that relies heavily on controlled heat and pressure. One of the most critical parameters in this process is mold temperature, which plays a vital role in the curing behavior, dimensional accuracy, and mechanical properties of the final thermoset part.
This article explores the ideal temperature ranges for thermoset molds, how temperature impacts the compression molding process, and specific considerations for materials like SMC (Sheet Molding Compound) and BMC (Bulk Molding Compound).
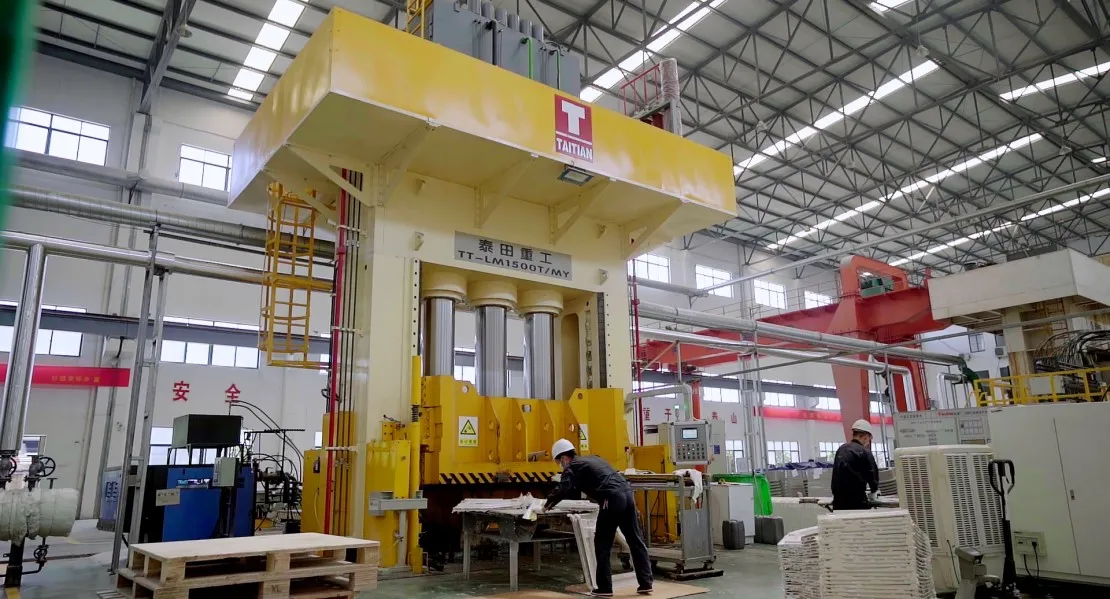
Understanding Thermoset Molding
Thermoset molding involves materials that undergo an irreversible chemical crosslinking reaction when exposed to heat and pressure. Once cured, these polymers cannot be remelted, making them ideal for structural applications that demand high heat resistance, mechanical strength, and dimensional stability.
Common thermoset materials include:
- Sheet Molding Compound (SMC)
- Bulk Molding Compound (BMC)
- Epoxy resins
- Phenolic resins
- Melamine and urea-formaldehyde resins
- Unsaturated polyester resins (UPR)
Ideal Mold Temperature Range for Thermoset Molding
The temperature of a thermoset mold typically ranges between 120°C to 200°C (248°F to 392°F) depending on the type of thermoset resin and the desired curing time.
Thermoset Material | Recommended Mold Temperature |
---|---|
SMC (Sheet Molding Compound) | 140°C to 170°C |
BMC (Bulk Molding Compound) | 130°C to 160°C |
Epoxy Resin | 150°C to 180°C |
Phenolic Resin | 160°C to 190°C |
Melamine/Urea Resins | 130°C to 150°C |
Factors Influencing Thermoset Mold Temperature
- Material Type and Thickness: Thicker or filled materials may require higher mold temperatures.
- Cure Time: Faster cycles need higher temperatures, but at the risk of defects like flash or burning.
- Mold Design: Complex compression or composite molds may need zoned heating.
- Surface Quality: Higher temperatures result in smoother surfaces and easier demolding.
Heating Systems in Thermoset Molding
Heating systems in thermoset compression molding include:
- Electric Cartridge Heaters
- Hot Oil Circulation
- Steam Heating
- Infrared Heating
These systems ensure uniform heating of SMC molds, BMC molds, and carbon fiber molds.
Importance of Precise Mold Temperature Control
Correct mold temperature control ensures:
- Complete resin curing and crosslinking
- Dimensional accuracy and mechanical strength
- Minimal surface defects and flash
- Longer mold life and lower maintenance
Applications That Rely on Thermoset Mold Heating
- Automotive: Battery covers, engine parts using SMC and carbon fiber compression molds
- Electrical: Insulating components produced with BMC molds
- Aerospace: Lightweight composite mold interiors
Comparison: Thermoset vs Thermoplastic Mold Temperature
Property | Thermoset Molding | Thermoplastic Molding |
---|---|---|
Mold Temperature | 120°C – 200°C | 40°C – 120°C |
Curing Behavior | Irreversible crosslinking | Physical melting and solidification |
Cycle Time | Longer | Shorter |
Heat Resistance | Excellent | Moderate |
Future Trends in Thermoset Mold Temperature Control
- Smart heating with AI-based feedback
- Induction heating and energy-saving technologies
- Zoned and adaptive heating for complex geometries
- Integration with digital twins and Industry 4.0
Conclusion
Understanding the ideal thermoset mold temperature is key to mastering the compression molding process. By maintaining proper temperatures in SMC molds, BMC molds, and other composite molds, manufacturers can achieve higher quality, greater efficiency, and reduced waste in thermoset production.