Thermoset molding is a critical manufacturing process to produce high-performance parts that require durable and heat-resistant properties. This molding process is widely used in industries such as automotive, aerospace, electrical, and consumer goods. In this article, we will explore the concept of thermoset molding, its benefits, applications, and the types of thermoset materials used in various molding processes.
What is Thermoset Molding?
Thermoset molding, also known as thermoset plastic molding, refers to the process of molding thermoset polymers into desired shapes using heat and pressure. Unlike thermoplastics, which can be remelted and reshaped many times, thermosets undergo a chemical change when exposed to heat. This curing process, also known as crosslinking, results in a rigid, permanent structure that cannot be remelted or reshaped.
Once thermoset polymers are cured, they become hard, stable, and resistant to high temperatures, chemical exposure, and wear and tear. The thermoset molding process is often used for applications that require these properties, making it ideal for producing components such as electrical enclosures, automotive parts, and industrial machinery.
The Thermoset Molding Process
The thermoset molding process involves several key steps, each of which is critical to the production of high-quality molded parts. Here's an overview of the general process:
- Preparation of Materials: The thermoset resin is mixed with other ingredients such as fillers, hardeners, and stabilizers to form a compound known as the molding material. This mixture may be in the form of powder, liquid, or preformed pellets, depending on the specific molding process.
- Injection/Compression Molding: In injection molding, the thermoset compound is injected into a mold cavity using an injection press. In compression molding, the compound is placed in an open mold and the mold is closed under pressure. The high heat in the mold initiates the curing reaction that transforms the material into a solid, cross-linked structure.
- Curing: The mold is heated to a specific temperature that activates the curing agent in the thermoset resin. This causes the polymer chains to chemically bond, forming a rigid and durable material. Cure time and temperature depend on the specific thermoset resin being used.
- Cooling and Ejection: Once the curing process is complete, the mold is cooled and the cured part is ejected. The part is then inspected for quality before being used in further assembly or finished product manufacturing.
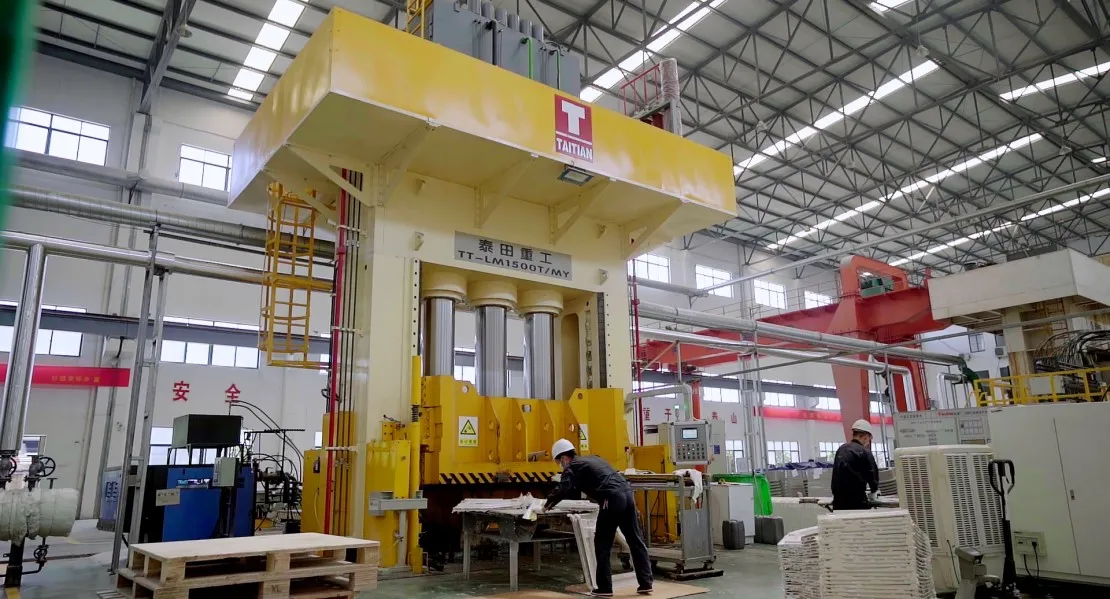
Types of Thermoset Materials
There are several types of thermoset materials that offer distinct advantages for different applications. Some of the most common thermosets include:
- Epoxy Resins: Epoxy resins are widely used in thermoset molding because of their excellent adhesion, chemical resistance, and durability. They are commonly used in electronics, automotive components, and coatings.
- Phenolic Resins: Phenolic resins are known for their high heat resistance, electrical insulation properties, and flame retardancy. These materials are often used in automotive, electrical, and industrial applications where high temperatures and harsh environments exist.
- Polyester Resins: Polyester resins are commonly used in molding that require good mechanical properties and chemical resistance. They are used in a variety of industries including automotive, marine and construction.
- Vinyl Ester Resins: Vinyl ester resins are a hybrid of epoxy and polyester resins that provide superior strength and corrosion resistance. They are used in applications such as piping systems, water tanks, and industrial components exposed to harsh chemicals.
- Melamine Formaldehyde: Melamine Formaldehyde is a thermoset material known for its hardness and heat resistance. It is commonly used in the manufacture of kitchenware, countertops and electrical insulation.
- Polyurethane (PU) Resins: Thermoset polyurethane resins are highly versatile, offering a wide range of mechanical and thermal properties. They are used in automotive parts, coatings, and elastomers.
Advantages of Thermoset Molding
Thermoset molding offers a variety of benefits that make it a preferred choice in industries where high performance and durability are required. Some of the key benefits include:
- High Thermal Resistance: Thermoset materials can withstand extremely high temperatures without deforming or losing their structural integrity. This makes them ideal for use in automotive, aerospace, and electrical components exposed to high heat environments.
- Chemical Resistance: Thermosets are highly resistant to a wide range of chemicals, including solvents, acids, and oils. This makes thermoset molding ideal for parts used in harsh chemical environments.
- Mechanical Strength and Durability: Once cured, thermoset materials exhibit excellent mechanical strength, impact resistance, and dimensional stability. These properties make them suitable for producing durable parts that can withstand heavy use and wear.
- Electrical Insulation: Many thermoset materials offer excellent electrical insulation properties, making them ideal for components such as printed circuit boards, electrical enclosures, and connectors.
- Environmental Resistance: Thermosets are resistant to moisture, UV radiation, and environmental degradation. This makes them well suited for outdoor applications and products exposed to the elements.
- Complex Geometries: The thermoset molding process allows for the creation of complex, intricate part geometries, making it possible to produce parts with high precision and fine detail.
Applications of Thermoset Molding
Thermoset molding is used in a wide variety of industries due to the versatile properties of thermoset materials. Some of the major applications include:
- Automotive Industry: Thermosets are used in the production of high-strength automotive parts, including engine components, electrical enclosures, dashboard parts, and structural elements. Their heat resistance and durability are essential for automotive applications.
- Aerospace Industry: In the aerospace industry, thermoset molding is used to produce lightweight yet durable parts such as wing components, fuselage panels, and engine covers. The high thermal resistance and strength-to-weight ratio of thermoset materials make them ideal for aerospace applications.
- Electrical and Electronics: Thermosets are commonly used for electrical enclosures, circuit boards, connectors, and switches. Their electrical insulating properties make them essential for preventing electrical malfunctions and ensuring safety.
- Consumer Goods: Thermoset molding is also used to create household products such as kitchenware, countertops, and electrical appliances. Durability and resistance to wear and tear make thermoset materials a good choice for everyday consumer products.
- Industrial Machinery: Components such as bearings, seals, gaskets, and other machine parts made from thermoset plastics offer high performance under heavy loads and harsh operating conditions.
- Construction: Thermosets are also used in construction for applications such as pipes, insulation, and structural components due to their high strength, chemical resistance, and environmental durability.

Challenges of Thermoset Molding
While thermoset molding offers many advantages, there are also some challenges associated with the process:
- Irreversible Curing: Once the thermoset material has been cured, it cannot be reshaped or reprocessed. This limits the ability to recycle thermoset materials and can result in waste during the manufacturing process.
- Longer Curing Times: Compared to thermoplastics, thermosets can take longer to cure, which can affect production speed and lead to higher manufacturing costs.
- Tooling Costs: The molds used for thermoset molding can be more expensive to manufacture due to the need for high-precision and high-temperature materials. In addition, the molds may need to be replaced more frequently due to the wear and tear caused by the curing process.
Conclusion
Thermoset molding is an essential process in manufacturing high-performance components used in a wide range of industries. The unique properties of thermoset materials, such as their high thermal resistance, chemical stability, and mechanical strength, make them ideal for applications that require durability and reliability under extreme conditions. While there are challenges associated with the process, the benefits far outweigh the drawbacks, especially in applications where performance is critical.
By understanding the intricacies of thermoset molding, manufacturers can better utilize these materials to create innovative, long-lasting products. Whether in automotive, aerospace, electronics, or consumer products, thermoset molding plays a key role in ensuring that the components we rely on every day continue to perform at the highest level.