Carbon Fiber Compression Molds - Carbon Fiber Autoclave Molds and Mold Process Analysis
- Suase /
- SUASE NEWS
Introduction to Carbon Fiber Compression Molds
Carbon fiber compression molds are key tools used in the manufacturing of high-performance composite products, widely applied in aerospace, automotive, medical devices, sports equipment, and other fields. Compared to traditional metal molds, carbon fiber molds are lighter, more heat-resistant, and exhibit excellent precision and stability.
Common types of carbon fiber molds include:
- Carbon Fiber Autoclave Molds: Suitable for high-temperature and high-pressure curing processes, ensuring product density.
- Carbon Fiber Compression Molds: Used for rapid forming, high production efficiency, and suitable for batch production.
- Composite Carbon Fiber Molds: Combining various material properties to enhance mold durability.
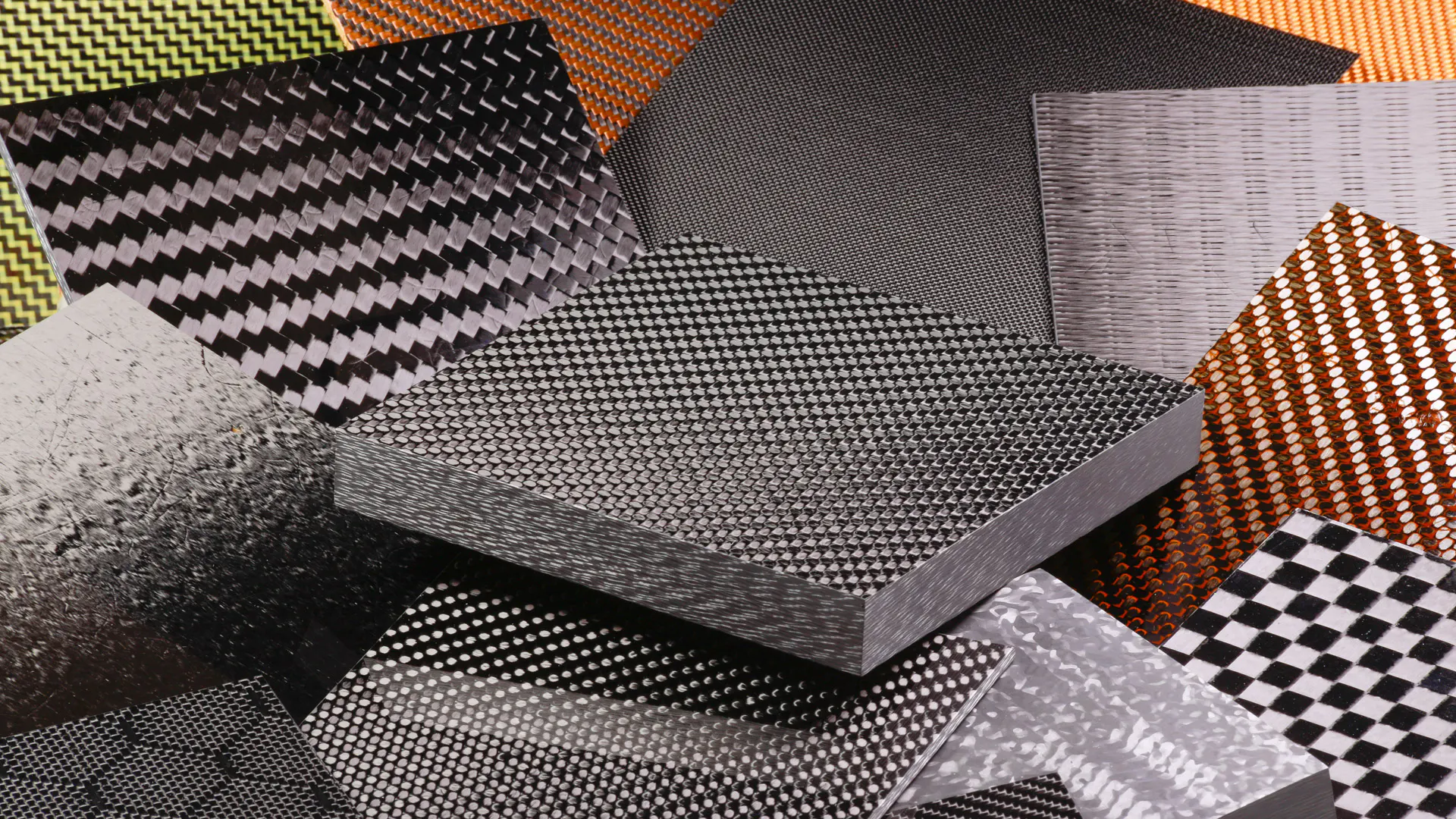
Advantages of Carbon Fiber Molds
Compared to traditional metal molds, carbon fiber compression molds offer the following core advantages:
- Lightweight: Carbon fiber's density is much lower than that of metal, making the mold easier to handle and more efficient for production.
- High-Temperature Resistance: Capable of withstanding temperatures above 200°C, suitable for high-temperature curing molding processes.
- High Strength: Strong impact resistance, maintaining shape over long-term use.
- Corrosion Resistance: Carbon fiber is unaffected by moisture, acids, or alkalis, making it suitable for harsh environments.
- Long Mold Lifespan: More durable than traditional metal molds, reducing replacement costs.
Carbon Fiber Mold Manufacturing Process
The manufacturing process of carbon fiber molds involves several key steps to ensure excellent precision and durability of the final mold:
- Mold Design: CAD modeling based on product requirements, optimizing structure and dimensions.
- Mold Manufacturing: Using CNC machining, 3D printing, or traditional hand-carving to create the mold prototype.
- Carbon Fiber Layup: Choosing appropriate carbon fiber prepreg materials and laying them up in layers.
- Autoclave Curing: Curing under high-temperature and high-pressure conditions to ensure mold strength and stability.
- Precision Machining and Surface Treatment: Includes polishing and coating treatment to improve surface finish and wear resistance.
Industry Applications of Carbon Fiber Molds
Carbon fiber compression molds are widely used in several high-end manufacturing fields:
- Aerospace: Aircraft fuselage, satellite components, high-strength structural parts.
- Automotive Manufacturing: Carbon fiber car bodies, bumpers, engine hoods.
- Medical Devices: X-ray tables, rehabilitation equipment, medical device housings.
- Sports Equipment: Carbon fiber bicycle frames, golf clubs, tennis rackets.
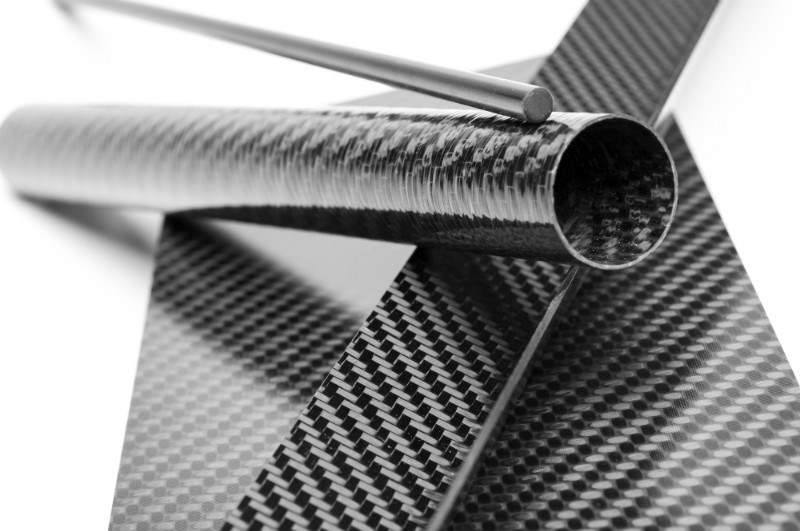
How to Choose a Carbon Fiber Mold Manufacturer?
Choosing the right carbon fiber mold manufacturer is crucial for ensuring product quality. Here are some key factors to consider:
- Experience and Technology: Quality manufacturers typically have rich production experience and advanced mold manufacturing technologies.
- Processing Capability: Whether the manufacturer has CNC precision processing and automation production capabilities.
- Mold Materials: Whether high-quality carbon fiber prepreg materials are used to ensure mold strength and longevity.
- Customer Cases: Review the manufacturer’s successful cases to evaluate its reliability.
- After-Sales Service: Quality manufacturers offer complete mold maintenance and technical support.