What is a Composite Mold?
Composite molds are specially designed molds used in the production of composite materials. These molds allow for the shaping of composite components that often require high strength-to-weight ratios and durability. Unlike traditional molds, composite molds utilize a combination of materials, including polymers and fibers, to achieve superior mechanical properties.
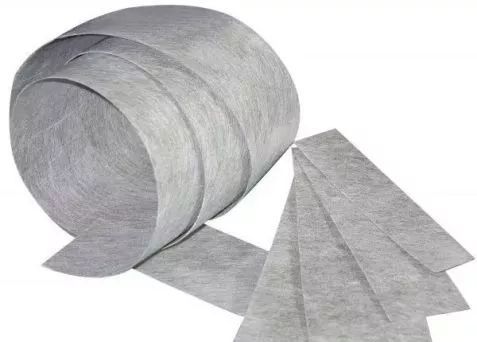
The Importance of Composite Molds in Manufacturing
Composite molds play a critical role in various industries, including aerospace, automotive, and construction. They are utilized for products like the SMC Water Tank, SMC Ceiling, and SMC Battery Cover, providing manufacturers with the flexibility to produce lightweight and robust parts.
Benefits of Composite Molds
- High Strength and Lightweight: Composite molds provide excellent strength while remaining significantly lighter than traditional materials, making them ideal for applications where weight reduction is crucial.
- Durability: The materials used in composite molds exhibit excellent resistance to environmental factors, such as moisture and temperature changes.
- Design Flexibility: Composite molds can be engineered to create complex shapes, allowing for innovative designs that are difficult to achieve with conventional molds.
- Cost-Effectiveness: While the initial investment may be higher, the longevity and reduced maintenance requirements can lead to lower overall production costs.
Types of Composite Molds
Composite molds can be classified based on the manufacturing process and the types of composites produced:
1. Compression Molds
Compression molds are widely used for shaping composite materials through the application of heat and pressure, particularly beneficial for Sheet Molding Compound Molds and BMC Molds.
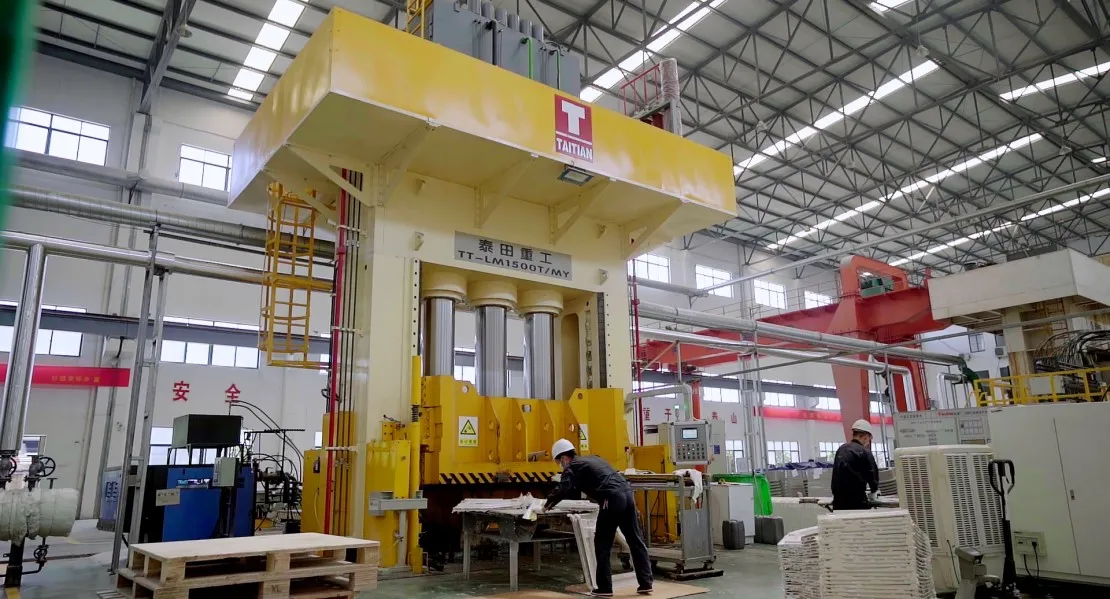
2. Injection Molds
Injection molding allows for precise control over the material's flow, making it suitable for producing detailed components, such as the Engine Splash Shield Mold or the EV Battery Enclosure.
3. Pultrusion Molds
In pultrusion, continuous fibers are pulled through a resin bath and into a heated die, forming long composite sections.
4. Vacuum Infusion Molds
This technique utilizes vacuum pressure to draw resin into a dry fiber layup, ensuring a high fiber-to-resin ratio and minimizing voids.
Applications of Composite Molds
Composite molds are employed in a range of applications, thanks to their versatility:
- Aerospace Components: Lightweight parts such as wing structures and fuselage sections.
- Automotive Industry: Components like the SMC Bathroom, which require durability and resistance to environmental stressors.
- Infrastructure: Building materials and fixtures designed to withstand harsh conditions.

Key Considerations for Choosing Composite Molds
When selecting composite molds for your project, consider the following:
- Material Compatibility: Ensure the mold material is suitable for the specific composite being used.
- Production Volume: Higher production volumes may justify the investment in more durable molds.
- Design Complexity: Consider whether the mold can accommodate the intricacies of your design.
Conclusion
Composite molds represent a significant advancement in manufacturing technology, providing high-performance solutions for a variety of applications. As industries continue to seek ways to reduce weight and increase efficiency, the demand for composite molds will only grow.
By understanding the benefits and applications of composite molds, manufacturers can make informed decisions to enhance their production processes and meet the evolving demands of the market.