GMT Compression Molding Technology: Process, Advantages, and Applications
- Suase /
- SUASE NEWS
GMT (Glass Mat Thermoplastics) compression molding is a composite material molding process that combines glass fibers and thermoplastic plastics. The process involves heating the composite material to a high temperature and then applying pressure to mold it into shape. It is widely used in industries such as automotive, aerospace, and construction. With the increasing demand for lightweight materials, GMT compression molding plays a crucial role in modern manufacturing.
1. Overview of GMT Compression Molding
GMT compression molding technology combines high-performance thermoplastic resins with glass fibers to form composite materials with high strength, corrosion resistance, and high-temperature resistance. These outstanding properties make it an ideal choice for many applications, especially in scenarios that require high strength and low weight. The technology utilizes precise molding equipment to efficiently manufacture complex components, widely used in automotive, aerospace, and construction fields, meeting the demand for high-performance materials in modern industries.
2. Process Flow of GMT Compression Molding
The basic process flow of GMT compression molding includes the following steps:
- Material Preparation: Select appropriate GMT composite materials, typically made by combining glass fibers and thermoplastic resins (such as PP, PE, etc.), which offer high strength and durability.
- Heating: Heat the composite material to a certain temperature to soften it, making it easier to mold.
- Compression Molding: Place the heated material into a mold and apply pressure to shape the material, completing the initial molding.
- Cooling and Demolding: After the molded part cools to room temperature, the demolding process is carried out to obtain the desired part shape.
- Post-Processing: After demolding, the part undergoes trimming, surface treatment, and other processes to meet the final quality standards.

3. Advantages of GMT Compression Molding
GMT compression molding technology has several significant advantages compared to traditional material processes:
- Lightweight Design: GMT materials have a much lower density than metal materials. Parts made from GMT materials are lighter than traditional metal parts, significantly reducing overall weight and energy consumption.
- High Strength and Rigidity: Enhanced by glass fibers, GMT materials possess excellent mechanical strength and rigidity, capable of withstanding large loads and pressures.
- Excellent Corrosion and High-Temperature Resistance: GMT materials perform excellently in harsh environments, especially in high-temperature and corrosive conditions, offering a longer service life than traditional metal materials.
- Electrical Properties: GMT materials have good electrical insulation properties, making them suitable for producing components for electrical and electronic devices.
- Efficient Production: The process has a short production cycle, making it suitable for large-scale production while reducing production costs.
4. Applications of GMT Compression Molding
GMT compression molding technology is widely applied in the following industries due to its lightweight and high-strength characteristics:
- Automotive Industry: GMT materials are widely used in automotive parts, such as body panels, bumpers, and door frames, helping to achieve automotive lightweighting and improving vehicle performance and fuel efficiency.
- Aerospace: The aerospace industry has extremely high requirements for lightweight and high-strength materials. GMT compression molding technology can provide high-performance materials that meet these demands, widely used in aircraft interiors, structural components, etc.
- Construction Industry: In the construction industry, GMT materials are used for exterior wall panels, roofs, floors, and other components, offering excellent corrosion resistance and high-temperature performance, making them suitable for various harsh weather conditions.
- Home Appliance Industry: Components such as casings and internal structures of home appliances can also be made using GMT compression molding technology, offering excellent electrical insulation and durability.
- Sports Equipment: GMT materials provide the necessary strength and lightness for sports equipment such as skis, skateboards, and boat hulls, ensuring high performance of the products.
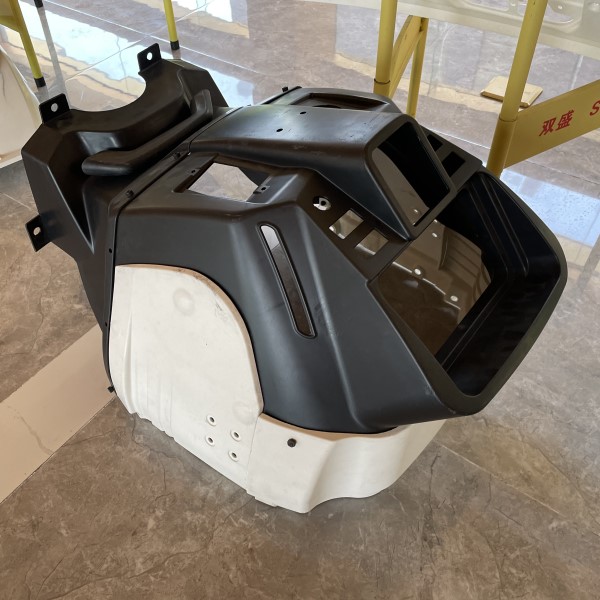
5. Challenges and Development Trends of GMT Compression Molding
Although GMT compression molding has significant advantages in various fields, it also faces some technical challenges:
- Material Cost: Compared to traditional plastic materials, GMT materials are more expensive, limiting their popularity in some low-cost applications.
- Recycling Issues: The recycling of GMT materials remains a challenge. With the increasing focus on environmental requirements, future innovations will be needed to improve their recyclability.
- Technical Requirements: GMT compression molding requires high-precision molding equipment, and the maintenance and operation of this equipment come with high technical demands.
In the future, with advancements in material science, the material performance and production efficiency of GMT compression molding will be further enhanced. At the same time, with the promotion of environmental policies, technological innovations will also make breakthroughs in sustainability.
6. Conclusion
GMT compression molding, as a new high-performance material molding technology, has become an essential technology in industries such as automotive, aerospace, and construction, owing to its outstanding advantages in lightweight design, high strength, and corrosion resistance. As production technology continues to progress, GMT compression molding will be applied in more industries, driving the innovation and development of global manufacturing.