Injection Mold Applications Explained: Automotive, Household, Appliance, and Logistics Molds
- Suase /
- SUASE NEWS
Injection molds are indispensable tooling in modern manufacturing, playing a vital role across automotive, household goods, home appliances, and logistics industries. Through efficient injection molding processes, mass production of plastic products is achieved while ensuring precision, consistency, and complex structures. This article explores the process characteristics, application advantages, and development trends of automotive injection molds, household goods injection molds, home appliance injection molds, and logistics injection molds.
I. Automotive Injection Molds: A Blend of High Precision and Durability
Automotive injection molds are widely used in the production of bumpers, grilles, lamp brackets, dashboards, interior panels, and other complex components. These molds are key to modern vehicle lightweighting and modular design.
- High-strength mold steels: Suitable for high-pressure injection and long production cycles. Common materials include H13, 718H, and S136.
- High-precision machining technology: CNC machining, EDM, and five-axis machining ensure mold precision and assembly consistency.
- Complex hot runner systems: Multi-point hot runners improve product appearance and structural integrity while reducing gate waste.
- Auxiliary structure design: Core pulling, hydraulic systems, and insert combinations facilitate molding of complex structures.
With the rise of smart and electric vehicles, automotive plastic parts are becoming more modular, lightweight, and intelligent, driving mold technology toward higher-end solutions.
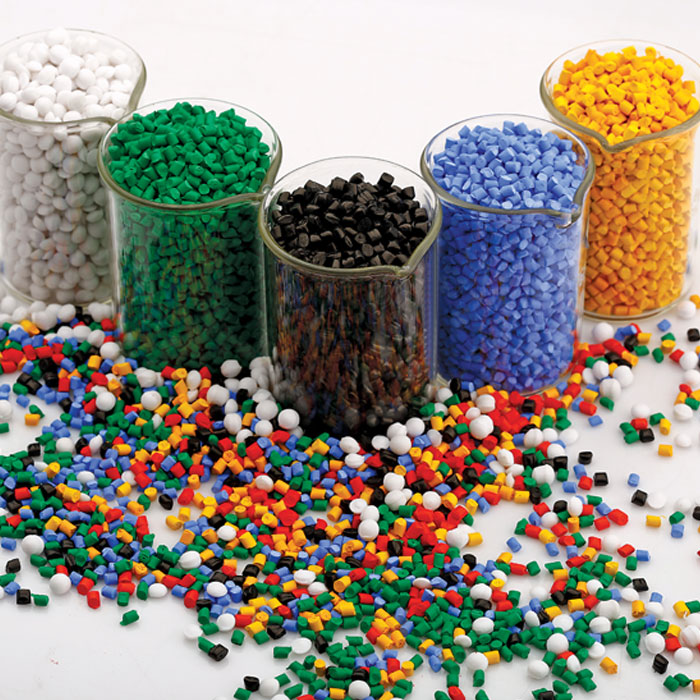
II. Household Goods Injection Molds: Efficiency and Diversified Production
Injection molds for household items emphasize multi-cavity design, fast cycles, and high mold durability. Common applications include cups, buckets, storage boxes, tableware, chairs, and trash bins.
- Simple mold structures: Easy maintenance and cavity replacement support product variety.
- Efficient cooling systems: Boost mold cooling speed and shorten molding cycles.
- Multi-cavity molding: Increases unit output and reduces operational costs.
- Eco-friendly plastic compatibility: Supports biodegradable materials such as PLA and PBS.
To meet personalized aesthetic demands, many manufacturers now adopt high-gloss electroplating, textured etching, and two-color injection techniques to optimize mold design.
III. Home Appliance Injection Molds: Precision Molding with Aesthetic Consideration
Plastic parts for home appliances demand strict mold requirements regarding dimensional accuracy, surface finish, and structural compatibility. Applications include refrigerators, air conditioners, televisions, washing machines, and rice cookers.
- High-polish surface treatment: Ensures excellent gloss for transparent components like panels and windows.
- Special texture etching: Molds can create leather grain, anti-slip patterns, and other visual effects.
- Modular design: Supports quick-change plug-in components for multiple model compatibility.
- Precision fitting: Ensures high-efficiency assembly of plastic and metal parts.
With CAE simulation and mold flow analysis, appliance molds can predict shrinkage, deformation, and weld lines, improving yield rate and reducing prototyping costs.
IV. Logistics Injection Molds: Durability and Structural Strength
Logistics plastic products require high load-bearing capacity, impact resistance, and long service life. Typical items include plastic pallets, turnover boxes, logistics baskets, and collapsible containers.
- Large-scale mold structures: Moving platens can exceed 2 meters, suitable for 3000T+ injection machines.
- Insert block design: Enhances thermal balance and mold longevity.
- Rib and stiffener designs: Improve product compression resistance and deformation control.
- Stack molds and rotary molds: Increase production flexibility and efficiency.
Modern logistics molds increasingly use high-toughness materials like P20 and 2738 steel and integrate smart temperature control systems for better performance and visualization.
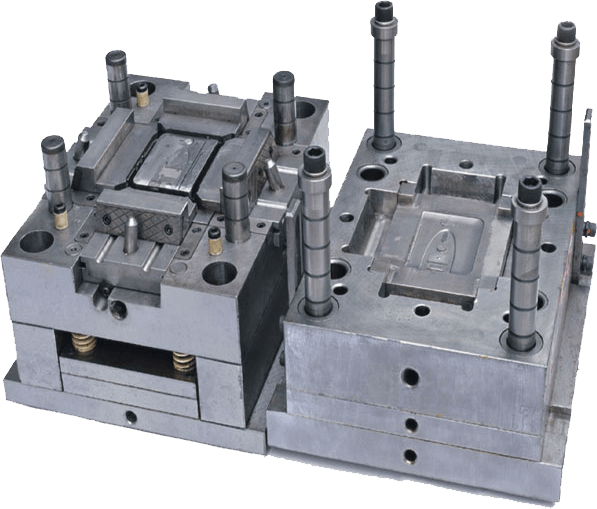
V. Development Trends and Selection Guidelines for Injection Molds
Today’s injection mold industry is moving toward smart manufacturing, digital management, high-performance materials, and green energy-saving solutions:
- Integration of IoT sensors enables remote monitoring and predictive maintenance.
- Digital twin systems facilitate virtual debugging and fault prediction.
- Eco-friendly cooling media and energy-efficient heating systems reduce carbon footprint.
- Modular mold customization enhances delivery efficiency and flexibility.
When choosing an injection mold supplier, companies should prioritize R&D capability, machining equipment, lead time, and service responsiveness. An experienced mold manufacturer not only customizes effective solutions but also significantly improves production stability and product quality.
For more solutions related to automotive injection molds, household goods injection molds, home appliance injection molds, and logistics injection molds, feel free to consult our professional mold engineering team.