PCM Composite Components: Driving the Development of the New Energy Industry
- Suase /
- SUASE NEWS
1. Overview of PCM Composite Materials
PCM (Prepreg Compression Molding) composite materials is an advanced composite manufacturing technology that uses prepreg for compression molding. It offers advantages such as lightweight, high strength, corrosion resistance, and high stability. This material is widely used in new energy vehicles, energy storage systems, and industrial equipment, making it a key material for the future of high-performance applications.
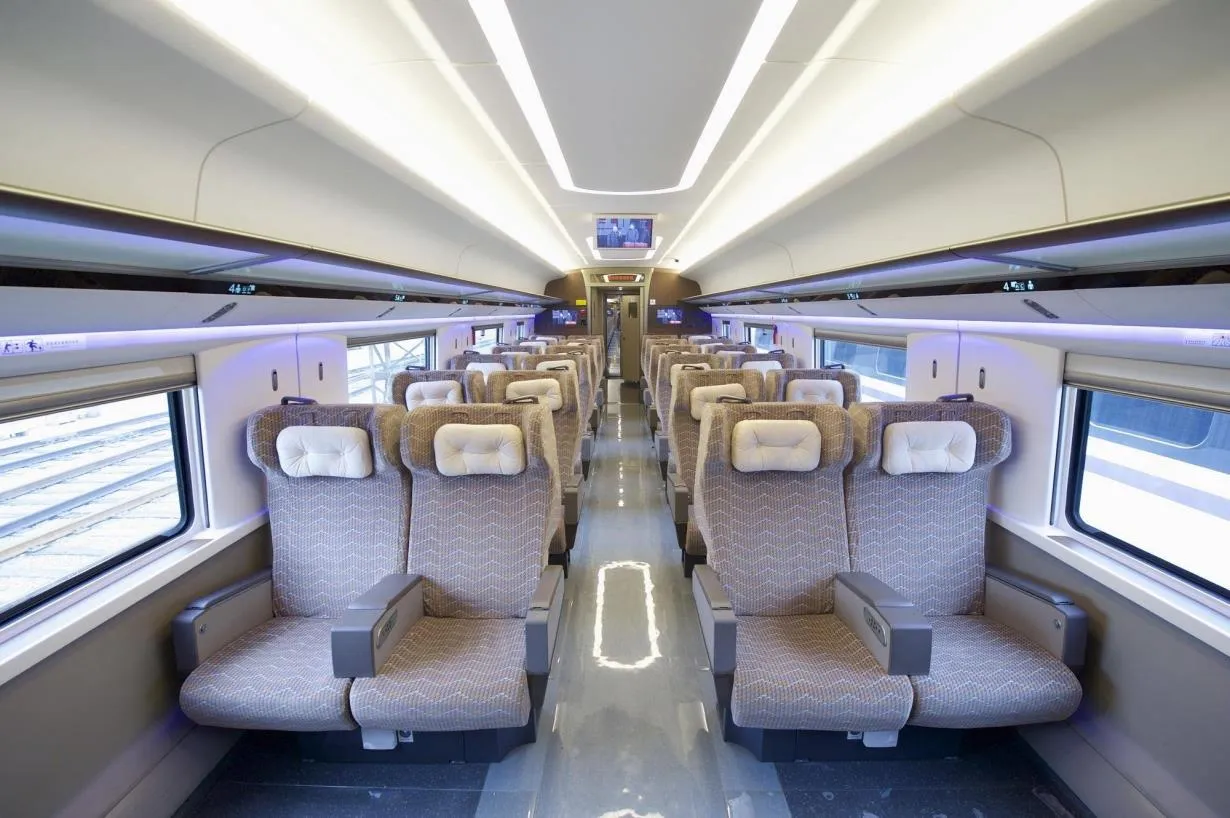
2. Advantages of PCM Composite Components
2.1 Lightweight Design
The density of PCM composite materials is much lower than that of metal materials, effectively reducing product weight and improving energy efficiency. For example, in the automotive industry, PCM materials can replace traditional metal components, reducing vehicle weight and extending driving range.
2.2 High Strength and Impact Resistance
PCM composite materials have excellent mechanical properties and strong impact resistance. They provide structural support and safety protection in applications such as new energy battery enclosures and energy storage boxes.
2.3 Corrosion Resistance and High Stability
Compared to traditional metal materials, PCM composites are resistant to moisture and chemicals, offering a longer lifespan. They are particularly suitable for energy storage devices and automotive components exposed to outdoor or harsh environments.
2.4 High Design Flexibility
PCM molding processes meet the requirements for complex structures and support customized production, making them suitable for components of various sizes and applications.
3. Applications of PCM Battery Enclosures
3.1 Enhanced Battery Safety
PCM composite battery enclosures feature high strength and heat resistance, effectively protecting battery cells from external impacts and improving overall battery safety.
3.2 Lightweight for New Energy Vehicles
Compared with traditional metal battery enclosures, PCM battery enclosures are significantly lighter, reducing overall vehicle weight, increasing electric vehicle range, and lowering energy consumption.
3.3 Excellent Insulation Properties
PCM materials have superior electrical insulation properties, effectively preventing short circuits and enhancing battery system safety.
4. Advantages and Applications of PCM Energy Storage Boxes
4.1 Improved Energy Storage System Safety
PCM composite energy storage boxes withstand extreme environmental conditions and have excellent fire-retardant properties, reducing thermal runaway risks and enhancing system stability.
4.2 Suitable for Various Energy Storage Scenarios
Whether for home energy storage, grid peak shaving, or industrial energy storage, PCM energy storage boxes provide lightweight, high-strength casing protection, ensuring long-term reliable operation.
5. Innovative Applications of PCM Automotive Components
5.1 Structural Automotive Parts
PCM composites are used in car doors, roofs, bumpers, and other parts, reducing overall vehicle weight and improving fuel efficiency or driving range.
5.2 Interior Components
PCM materials are used in dashboards, center consoles, and other interior components, offering better aesthetics and durability while maintaining eco-friendly properties.
5.3 Structural Support Components
PCM composite materials are applied to automotive chassis structures and brackets, enhancing vehicle safety, impact resistance, and durability.
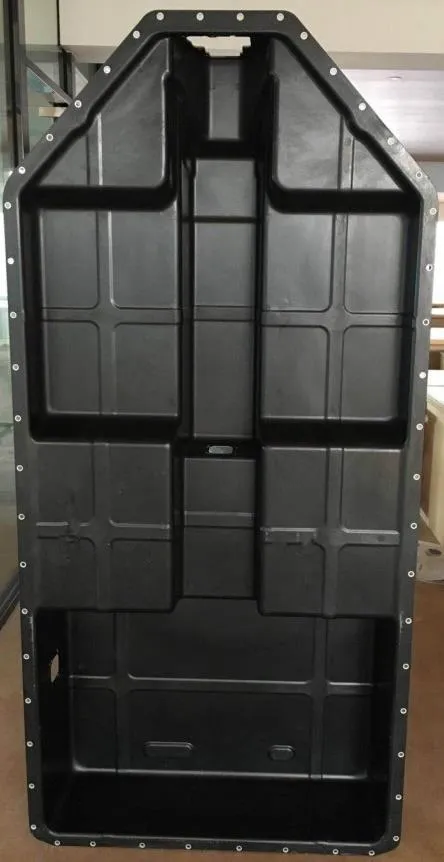
6. Future Prospects
PCM composite components have demonstrated significant advantages in battery enclosures, energy storage boxes, and automotive parts. With the rapid growth of the new energy industry, the application of PCM technology will become even more widespread, providing safer, lighter, and more efficient solutions. In the future, PCM composite materials will continue to drive the trends of lightweight and high-performance development, supporting the expansion of the global green energy industry.