What are PHC Molds?
PHC molds are specialized molds used to produce prestressed concrete components. Prestressed concrete (PHC) is a building material that enhances concrete strength by applying prestress, typically used in the construction of bridges, roads, power towers, and other structures. PHC molds are used to shape these concrete components, ensuring precise dimensions, smooth surfaces, and good mechanical properties.
The manufacturing requirements for PHC molds are high because they must withstand the high pressure during the concrete curing process and have sufficient wear and corrosion resistance. Therefore, PHC molds are typically made from high-strength steel to ensure they can be used continuously in the production process without being affected by environmental or operational conditions.
Main Features of PHC Molds
1. High Strength and Durability
One of the main features of PHC molds is their high strength and durability. Since prestressed concrete needs to withstand significant pressure, PHC molds must have strong mechanical properties to endure the stress during the concrete curing process without deformation.
2. Precise Dimensional Control
PHC molds ensure precise control of the dimensions of concrete components during production. Since prestressed concrete is widely used in construction structures requiring high precision and long-term use, any small errors could affect the final product's quality and performance.
3. Corrosion Resistance
PHC molds are typically made from steel or alloys with high corrosion resistance, effectively preventing the molds from corroding when in contact with concrete, thus extending the mold's service life.
4. Easy Demolding
Since concrete tightly adheres to the mold surface during the curing process, PHC molds are designed to facilitate easy demolding. Surface treatments and internal coating designs help ensure that the molds can be easily removed from the concrete components without damaging the product's surface.
5. High Temperature Resistance
The curing process of prestressed concrete requires relatively high temperatures, so PHC molds must have good high-temperature resistance to ensure they do not deform or become damaged during temperature changes.
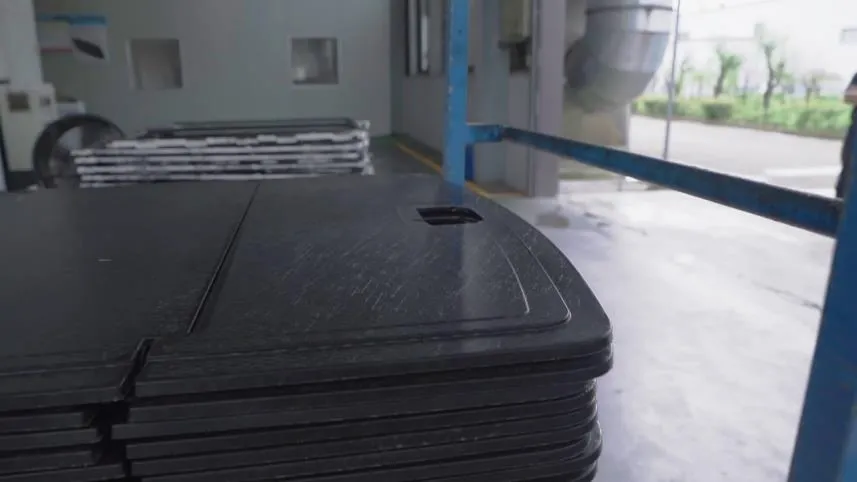
Applications of PHC Molds
1. Bridge Construction
PHC molds are widely used in bridge construction. Prestressed concrete components are used to make beams, slabs, and columns for bridges. Using PHC molds ensures that these components have sufficient strength and durability, thus improving the overall stability and safety of the bridge structure.
2. Road Construction
In road construction, PHC molds are used to produce various prestressed concrete components such as road slabs and bridge deck panels. These components need to withstand heavy traffic loads, so PHC molds are designed to meet the high strength and durability requirements.
3. Power Towers and Communication Towers
PHC molds are also widely used in the production of power towers and communication towers. Since these towers need to withstand strong winds and other environmental factors, prestressed concrete towers have high stability and wind resistance. The accuracy of the PHC molds directly affects the quality and safety of the tower structures.
4. Water Facilities
In water facility construction, PHC molds are used to produce key prestressed concrete components such as dams and water diversion channels. Prestressed concrete, known for its high strength and compression resistance, is ideal for these crucial components, which require high precision and long-term durability.
5. Other Infrastructure Projects
In addition to the applications above, PHC molds are also used in various other infrastructure projects, such as tunnels, underground pipelines, and road bridges. Due to their high strength and durability, PHC molds meet the strict requirements for materials and structures in large-scale construction projects.
How to Choose the Right PHC Mold
1. Material Selection
PHC molds should be made from materials with good strength, wear resistance, and corrosion resistance. Typically, high-quality steel or alloy materials are the first choice for PHC molds, as they can withstand the pressure from concrete and are not easily damaged.
2. Design Precision
The design precision of PHC molds directly affects the final quality of the concrete components. When selecting molds, it is essential to ensure that the mold design meets the required dimensions and ensures smooth, flawless surfaces for the concrete components.
3. Demolding Performance
The demolding performance of PHC molds is critical. The smoothness of the mold surface, coating design, and internal structure all contribute to easy demolding, avoiding damage to the concrete component’s surface or shape.
4. Production Efficiency
Different types of PHC molds may have different production efficiencies. When selecting molds, consider the production needs and cycle time, choosing molds that allow for fast and efficient production to enhance overall productivity.
5. Durability and Maintenance
Since PHC molds are often used under harsh working conditions, it is essential to choose molds with high durability and easy maintenance. Regular maintenance and inspection can extend the mold’s service life.
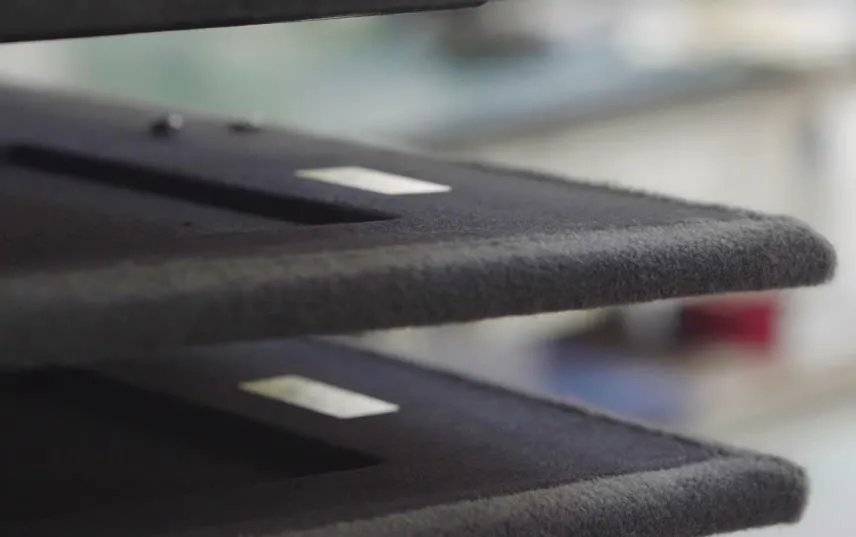