Comprehensive Analysis of SMC Molds: High-Performance Composite Compression Molding Solutions
- Suase /
- SUASE NEWS
With the widespread application of composite materials in construction, automotive, electrical, telecommunications, and sanitary ware industries, SMC molds (Sheet Molding Compound) have become increasingly vital as key forming tools. SMC compression molds offer excellent mechanical properties, high insulation, outstanding corrosion resistance, and efficient mass production capabilities, making them a crucial supporting technology across various industries.
What is an SMC Mold?
SMC molds are metal molds used for hot compression molding of sheet molding compounds, compatible with high-tonnage hydraulic presses for high-temperature and high-pressure production. These molds can achieve one-time forming of complex structural parts, offering advantages such as high strength, lightweight, and high design flexibility. They are widely used in manufacturing high-performance parts for industrial and consumer applications.
Typical Applications of SMC Molds
Electrical & Telecommunications
- SMC electrical box mold, SMC meter box mold, SMC junction box mold, SMC distribution box mold
- SMC cable bracket mold, SMC insulator mold, SMC antenna mold
The electrical and telecommunications industry demands high insulation, corrosion resistance, and weatherability. SMC materials naturally possess excellent performance, making them the ideal choice. Molds in this category require high sealing performance and multi-cavity precision design.
Sanitary Ware
- SMC wash basin mold, SMC laundry sink mold, SMC bathtub mold, SMC shower tray mold, SMC bathroom mold
SMC sanitary products are aesthetically pleasing, lightweight, stain-resistant, and pressure-resistant, making them suitable for modern home decoration and engineering projects. The molds must feature mirror polishing to meet the high standards of the sanitary ware industry.

Construction & Municipal
- SMC door panel mold, SMC standard door mold, SMC water tank panel mold, SMC manhole cover mold
The construction sector emphasizes structural strength and corrosion resistance. SMC molds enable one-piece forming of door panels, water tank panels, and other components, improving construction efficiency and product durability.
Automotive Exterior Parts
- SMC truck exterior part mold, SMC bumper mold, SMC front grille mold, SMC car door mold, SMC trunk mold, SMC decorative panel mold, SMC footboard mold
The trend toward lightweight vehicles has driven the widespread use of SMC composites. SMC automotive molds support the precise and rapid production of high-rigidity exterior parts and can be pre-treated for painting.
Medical Equipment
- SMC medical mold
Medical molds must meet hygienic, non-toxic, and corrosion-resistant requirements. SMC molds can reliably form components such as hospital bed boards and diagnostic equipment housings.
Features of SMC Mold Manufacturing Process
- Five-axis machining with mirror polishing ensures molding accuracy and surface quality.
- Built-in exhaust system and temperature control enhance forming efficiency and stability.
- Optimized parting line design improves demolding smoothness and product aesthetics.
- High-strength steels such as P20, 718, and H13 are used to extend mold life.
Key Criteria for Selecting an SMC Mold Manufacturer
- Extensive experience in SMC compression mold development.
- One-stop service from design to mold delivery.
- Comprehensive quality control processes to ensure precision and longevity.
- Reliable after-sales support for long-term cooperation.
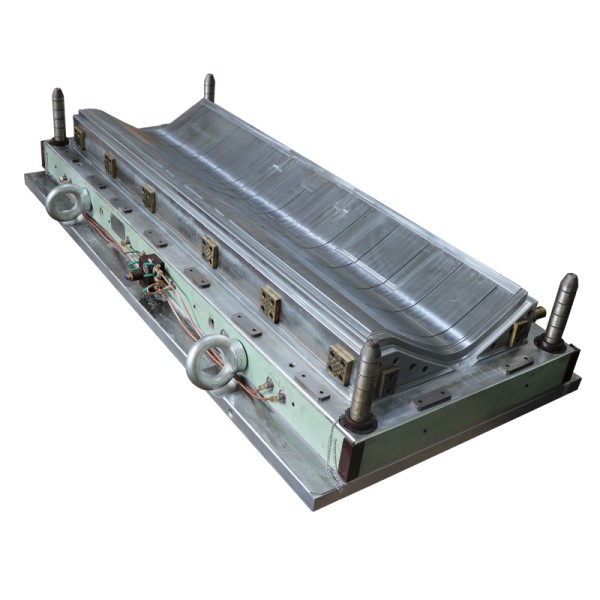
Future Trends of SMC Molds
With the rise of new energy, 5G communications, new infrastructure, and vehicle electrification, SMC molds are evolving toward larger sizes, greater integration, smarter technology, and automation. Mold manufacturers must continuously improve their technology and management capabilities to meet the rapid delivery needs of complex products.
Conclusion
Whether it's SMC meter box molds, SMC bathtub molds, or SMC truck exterior part molds, professional mold development capabilities are the core to ensuring product quality and production capacity. Choosing an experienced SMC mold manufacturer will help businesses stand out in the competitive market.